
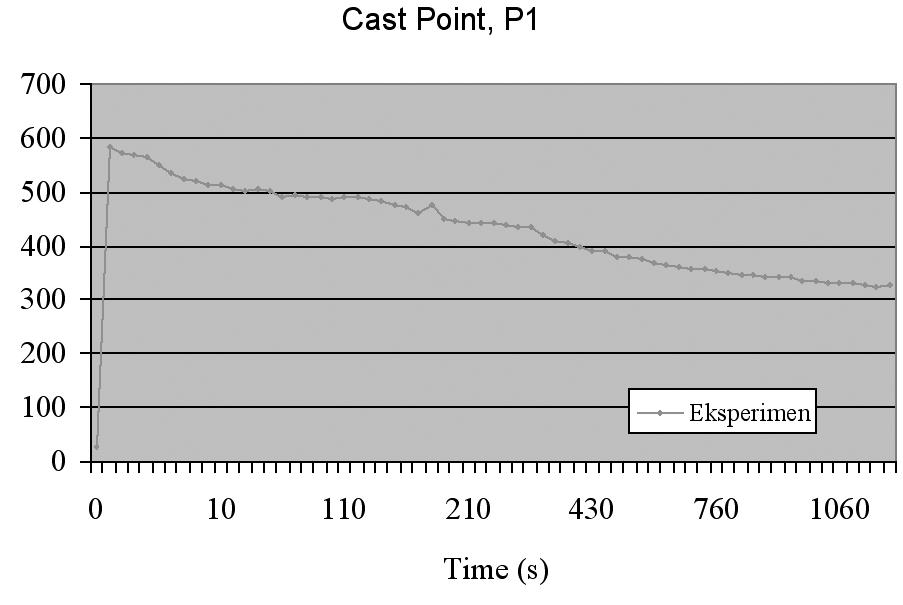
In particular, according to the well-known Hall-Petch relation, the finer the grain the harder is the material. As reported in Section 2.14.3.1.1 for the oxide ceramics there is a general agreement on the fact that a reduction of the grain size leads to an increase of wear resistance. For this reason, nanosized materials have been considered very promising substitutes for more conventional structural materials for tribological applications ( Andrievski, 2009 Gleiter, 1989 Hahn & Padmanabhan, 1995 Han, Lavernia, & Mohamed, 2005 Mukhopadhyay & Basu, 2007 Vassen & Stover, 2001 Weertman et al., 1999). Grain refinement usually implies better mechanical properties. Goffredo de Portu, Stefano Guicciardi, in Comprehensive Hard Materials, 2014 2.14.4.2 Grain Size In this work, it was noted that best nucleation formation results were obtained for inoculation periods lasting 2 min or more. By applying the higher pouring temperature, the grain refiner was able to provide a finer and more homogeneous microstructure with small variation in grain size between the center and the edge of the slug ( 108). For example, the addition of Al–5Ti–1B grain refiner into molten aluminum alloys has been found to be less effective at lower pouring temperature in the range of 630–650 ☌ compared to a higher pouring temperature range from 670 to 720 ☌ ( 108).
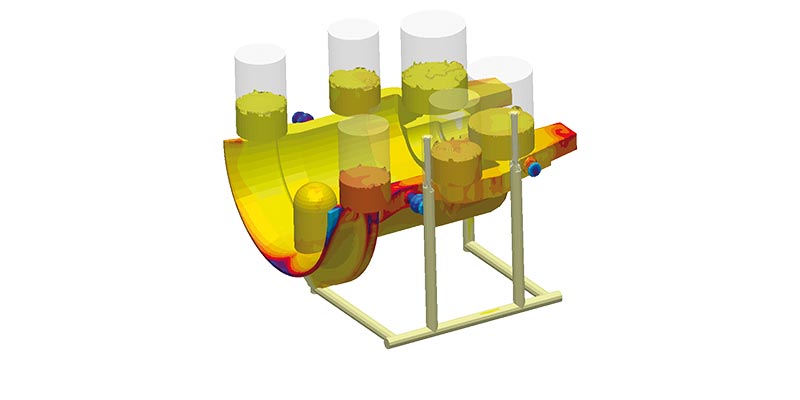
The reaction of grain refiner in this case was found to depend not only on the material used as the refiner but also on the processing temperature. Grain refinement has been combined with the NRC method of feedstock production ( 108, 109) The addition of Al–5Ti–1B chemical grain refinement into aluminum alloy Al–7Si–0.4 Mg reduces the size of the grains where the system requires a high melt pouring temperature. Brabazon, in Comprehensive Materials Processing, 2014 5.07.4.2 NRC with Grain Refinement
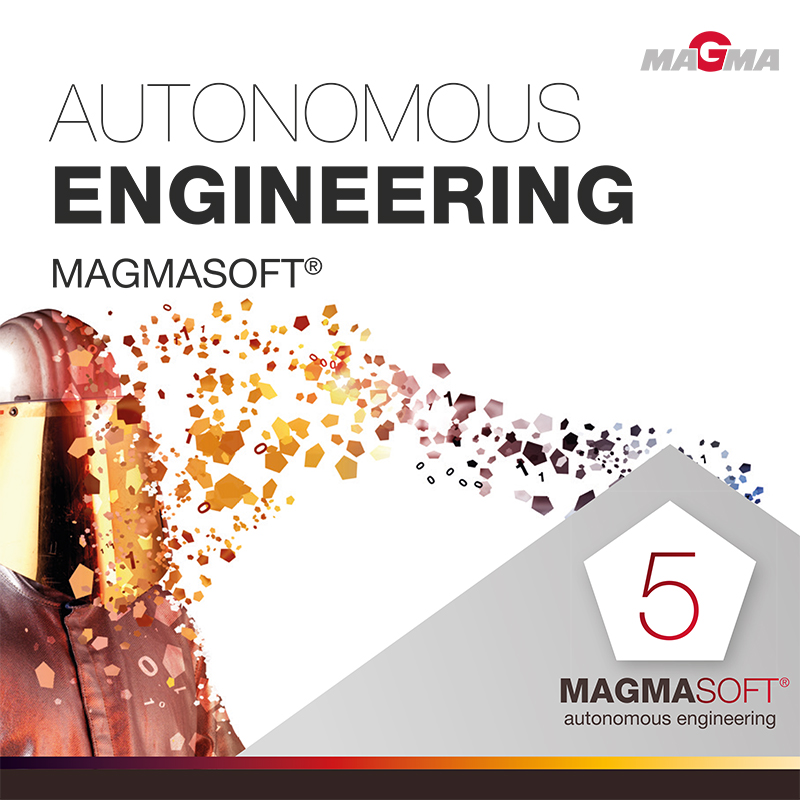
The tensile tests at an elevated temperature of 673 K were performed under the condition of strain rate from 1.0 × 10 − 4 s − 1 to 5.0 × 10 − 2 s − 1 to investigate the superplastic characteristics such as strain rate sensitivity index m and elongation.Ī.H. To observe the microstructure of AZ31 magnesium alloy, the samples were etched by picric acid solution. The forming temperature and extrusion ratio were 523 K and 6.4, respectively, in the experiment. For comparison, a billet not processed by ECAE was also processed by the extrusion. The extrusion process with a fixed mandrel for fabricating a tubular shape with outer and inner diameter of D = 2 mm and d = 1 mm, respectively, were carried out for the billets with fine grain after the ECAE process. Billets were processed by ECAE at 473 K for four passes via route B C ( Iwahashi et al., 1996). As a result of the pressing, the billet is subjected to simple shear state but retained the same cross-sectional area so that it was possible to repeat the pressings for several cycles. The ECAE process used is the technique of pressing specimens through a die containing two channels with diameter of 4.5 mm, equal in cross-section, intersecting at an angle of 90°. The initial average grain size of the billet is 9.3 μm. The billet used in the ECAE process has a diameter of 3.8 mm and length of 45 mm. Schematic illustration of grain refinement using the combined ECAE/Extrusion process for alloy tubes (units are mm).ĪZ31 magnesium alloy was used in the experiment. The effectiveness of the grain refinement and superplastic dieless drawing for fabricating magnesium alloy fine tubes is described.ġ4.18. Additionally, to fabricate the magnesium alloy fine tube, the dieless drawing process is applied for a magnesium alloy tube with fine grain by use of the combined ECAE and extrusion processes. In this section, the novel grain refinement method by combined ECAE and extrusion processes for tubular material was proposed. The grain refinement processing for tubular materials has not been studied. However, most conventional grain refinement methods covered bulk and sheet metals from the viewpoint of the shape of the target material. Many grain refinement methods have been suggested, such as ECAE (equal-channel angular extrusion) ( Iwahashi et al., 1996) and ARB (accumulative roll bonding) ( Lee et al., 2002). Grain refinement processing has become an attractive procedure for producing alloys with mechanical properties including high strength at room temperatures and a superplasticity at elevated temperature. Manabe, in Superplastic Forming of Advanced Metallic Materials, 2011 14.6.2 Grain refinement process for a metal tube
